Successful case of Smart Factory
Introducing examples of cutting-edge smart factory construction, which 3View has been leading in various industries.
Successful case of Smart Factory
Introducing examples of cutting-edge smart factory construction,
which 3View has been leading in various industries.
Toyota’s JIT
(Just-In Time → Pull system) on Production and Quality management
One of Tier company of Toyota Motor, who adapted 3View’s MES
and successfully has been worked year 2015 .
Especially worked well with Toyota’s Kanban system.(Pull system)
and tool management system.
Innovation awarded year 2017by Korean Government
48% reduction of quality problem. 7.5 % Productivity Up
* Smart Factory “Excellent Construction Case”
Winning the 2016 Manufacturing Innovation Award
* 3,000 items/ 400 million parts per month,
Tier 1 of General Motor and Hyndai Motor
“We now, became to be able to promptly take action in
problems regarding machines and bolts within 10 minutes.”
We’d not have imagined if we hadn’t adapted to “the smart factory project”.
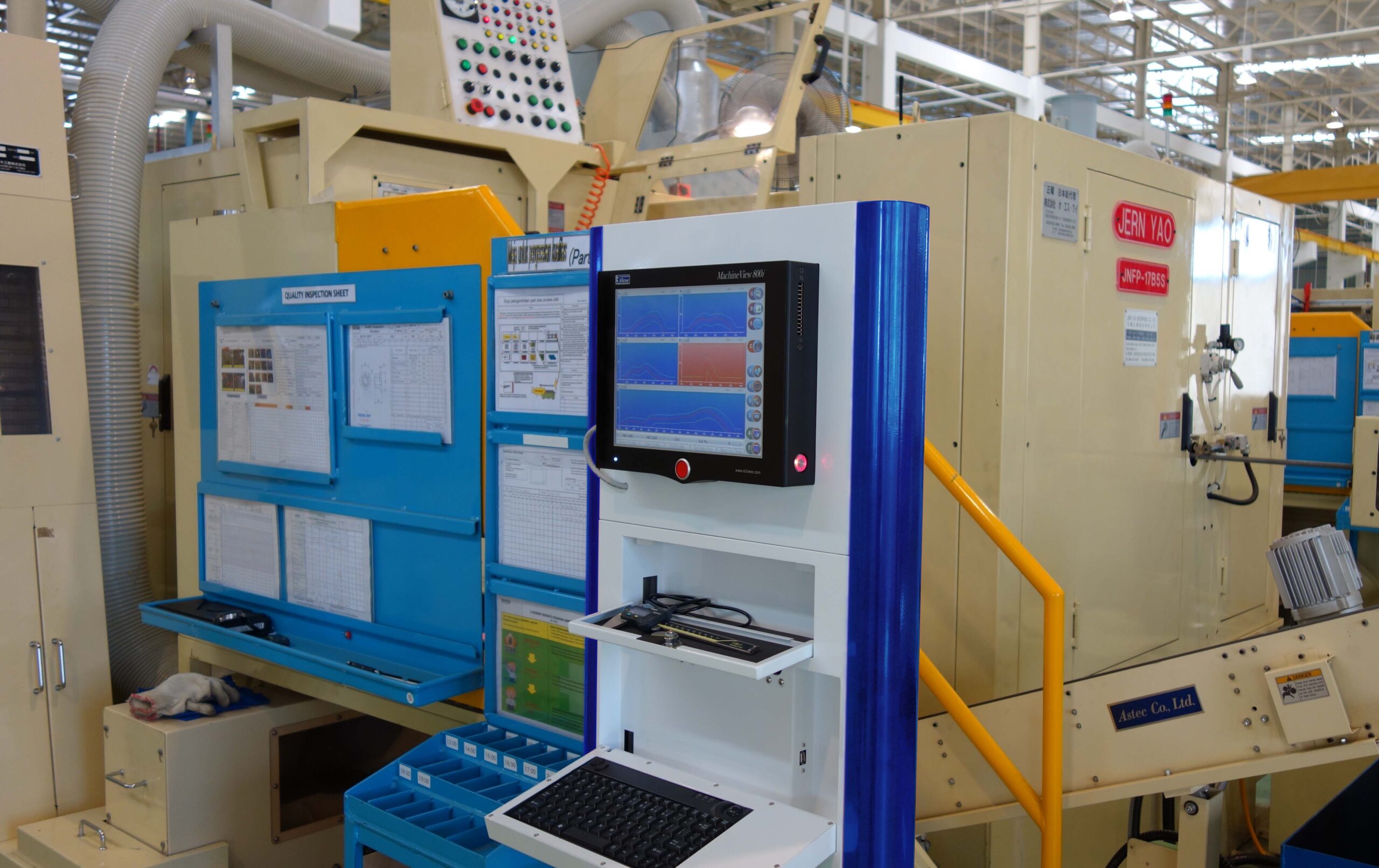
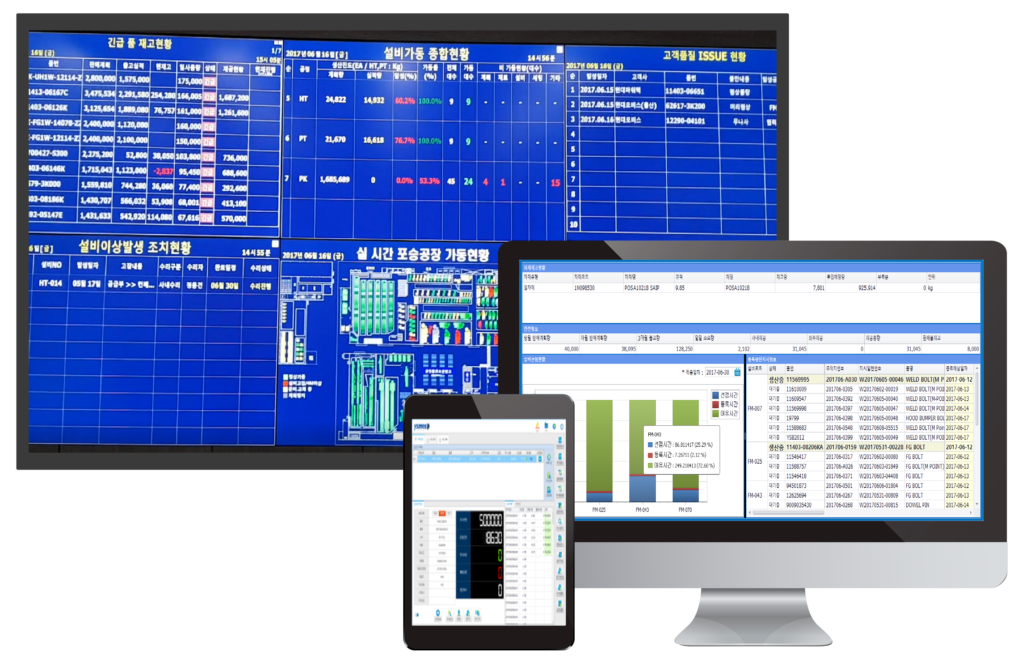
Smart Factory (2015~2017) with
Status board
Building FactoryView™ MES that oversees all processes
FactoryView™ was installed on year 2015~2016
Building FactoryView™ MES that oversees all processes
FactoryView™ was installed on year 2015~2016
Production planning –afterproduction, work-order management institution.
Production management – adaption to process LOT of the shape of batch manufacturing.
Outsourcing management – Distribution on SCM outsourcing program.
Quality management – first-middle-last standard-establishment and abnormal process control.
Tool management – automatic founding tool storage.
Machine management – adaption to afterwork-preservation and module for preservation management.
PDM – management planner, work standard sheet etc.. and stadardization on product history management and action to Five star.
Design and build a central control system
Introduced escalation-type Andon system through mobile alarm service
J company – sophisticated construction project.
Intelligent production planning establishment. Yearly, monthly project planning establishment. Planning based on dispatching rules.
Real-time collection for forging data. Collection for force data affiliated with Production management information.
Real-time data collection for Heat-treatment, surface treatment. Collection for OPC UA-based data affiliated with SCADA and monitoring. Control of In-put and work-condition.
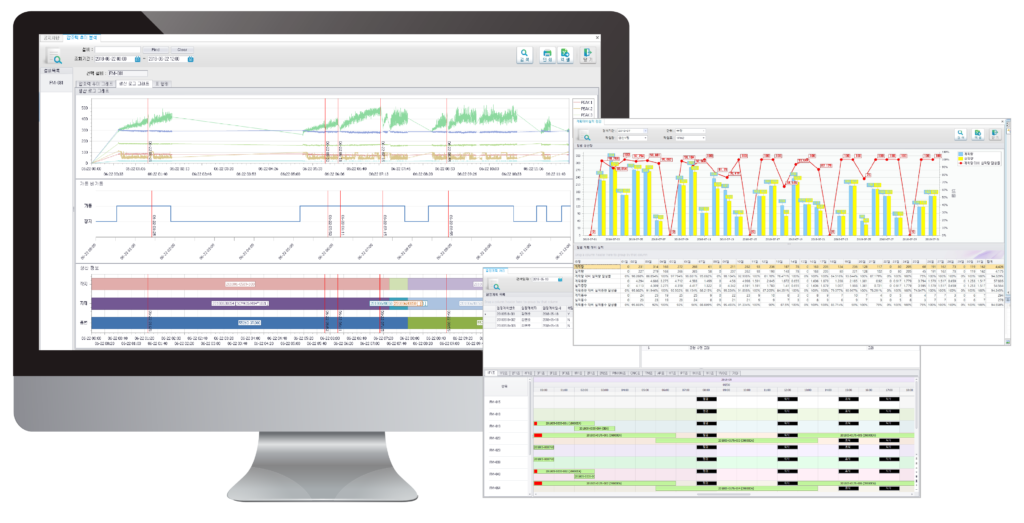
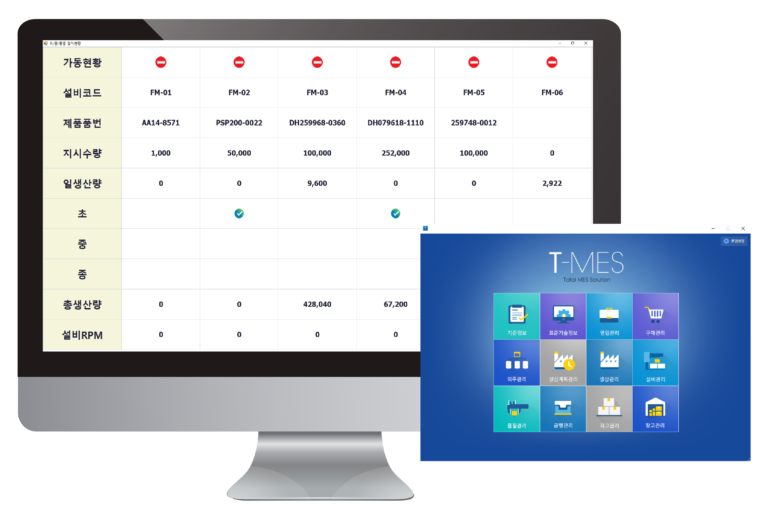
Construction project for smart factory (FactoryView™) (2016~2018)
Building FactoryView ™ MES that oversees all processes
– Production planning – monthly production plan adaption.
– Outsourcing – outsourcing management by the use of worker program.
(the outsourcing company can input the outsourcing production details)
– Quality management – standization for first-middle-last and control of work-in-process stock.
– Tool management – tool LOT adaption and interlocking with the counting details in real-time.
– Machine management – daily check management.
Institution of the new system which enables MachineView as a terminal for interlocking with former machines.
onstruction of “Zigbee” also known as wireless communication.
G company – information-oriented project ( 2014 ~ 2015 )
Building FactoryView ™ MES that oversees all processes
Push linear production management way system adaption through forge-work order.
Automatic production quantity counting system adaption by integration between MachineView™ and Zigbee.
Quality statistics management feature adaption which saves and analyzes real-time quality input data.
TRM(Maintenance and machine management) feature adaption.
* Enhance project includes setting IoT device to machine, interface between MES and MachineView™, was completed in 2018.
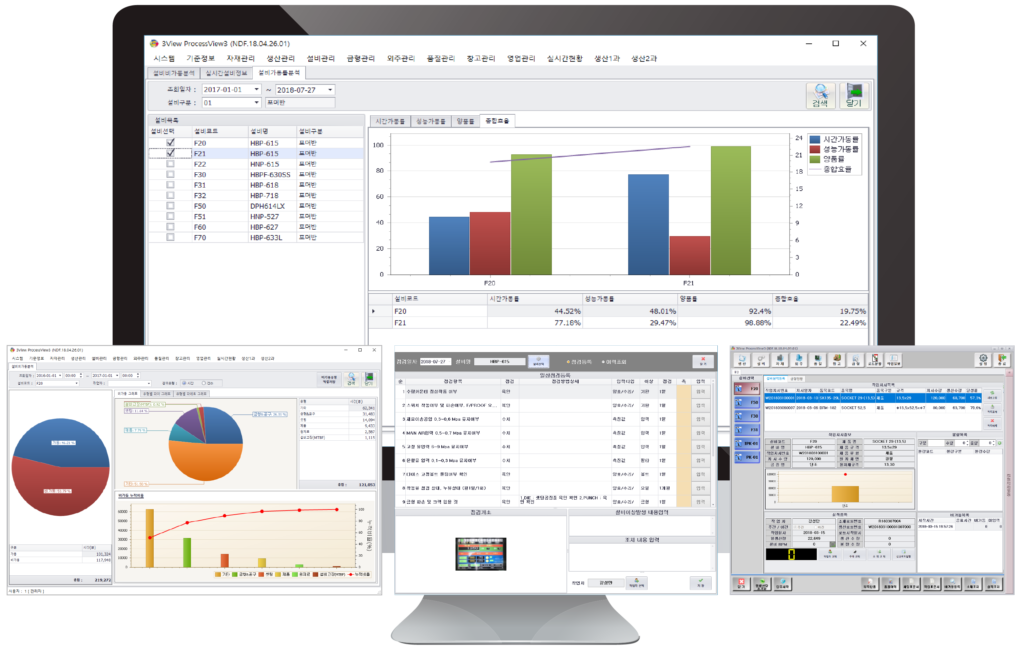
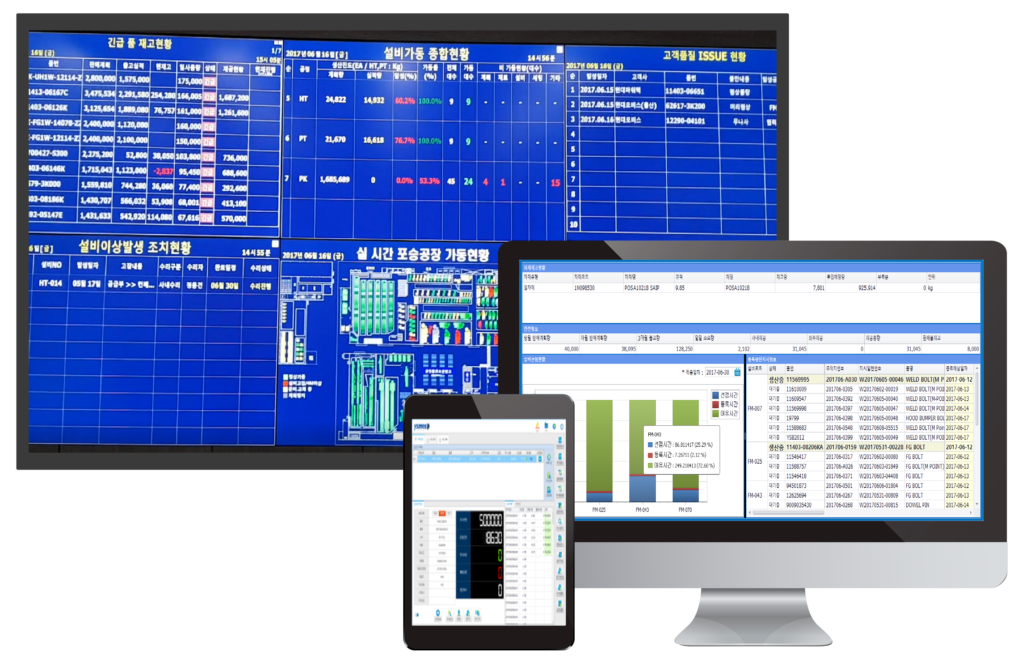
Smart Factory MES (FactoryView™) Project (2016~2018)
Building FactoryView ™ MES that oversees all processes
Establishment of main production plan (MPS) and material requirement plan (MRP)
Outsourcing management – SCM outsourcing warehouse management by interworking with outsourcing companies
(Outsourcing management entered directly by the outsourcing company)
Quality Management – Establishment of elementary, middle, and grade standards and introduction of abnormal work control function
Automatic interlocking of mold BOT (Bill of Tool) configuration and number of punches
Introduction of facility maintenance and daily inspection functions
Facility management – introduction of daily inspection management function
Introduction of a system using MachineView™ as a former interlocking terminal
Establishment of real-time operation information sensor network wireless communication network of facilities
D company provided with MachineView™ + SPOP ln China since 2016.
Quantity : 2 factories with 25 MachineView™ all adapted to SPOP
Development background
Change – the quality management way with naked eyes. Necessity for the suitable system before adaption to the computerized quality management called “POP, MES” Demand on better quality management solution.
Result
Quality improvement and prevention in advance about wrong products
through real-time monitoring system.
The managers become able to manipulate real-time check in SPOP system.
Better production management adaption through consultation on quality information standardization
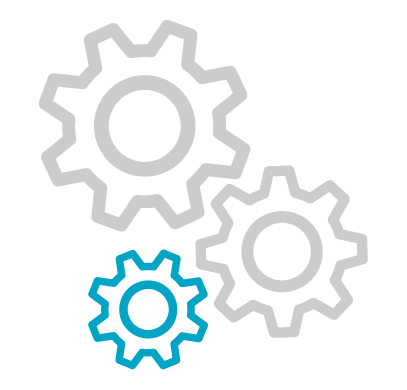