FactoryView™
MES
Manufacturing execution systems that contribute to productivity improvement and cost reduction through integrated management of data at production sites
FactoryView™ MES
By collecting all data from the production site in real time, It improves problems and contributes to improving quality, cost and productivity.
FactoryView™ MES is a Manufacturing Execution System (MES).
It collects data of the manufacturing process that occurs in real time, and quickly and accurately grasps the real-time situation in the field.
It is an essential solution for a smart factory that solves problems and contributes to quality, cost and productivity improvement.
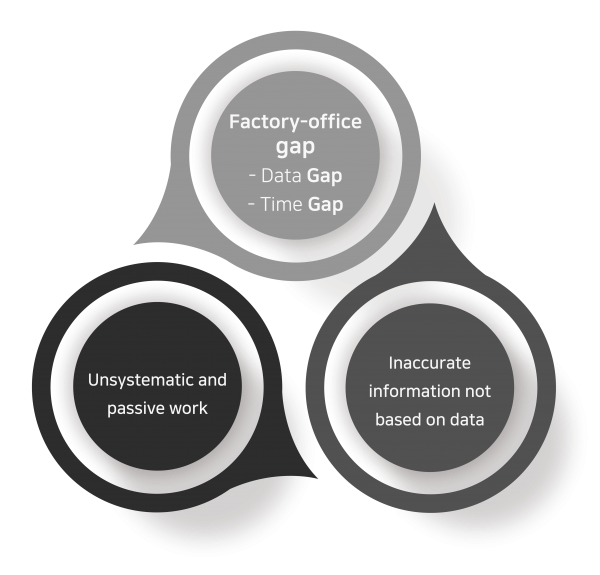
Before the introduction of MES
- Because data is written manually or in Excel,
it takes a lot of time and money to aggregate and manage. - Hard to find when a record is lost or needed.
- Work procedures are not standardized,
and vary from operator to operator. - It is difficult to immediately identify the occurrence
of a defect, and it takes time to deal with it. - It is difficult to manage inventory or supply and demand of materials.
- There is a lot of unused stock left and manufacturing costs
are consumed more than necessary. - Materials cannot be tracked
After the introduction of MES
- Production data can be aggregated in real time.
Production status can be grasped immediately in the field,
control room, and mobile. - It can check the current status of machine operation and
real-time product. - Quality inspection results can be collected automatically
and statistically analyzed. - All information from sales orders to product shipments
can be integrated and managed organically. - Semi-finished products or raw materials required for products
can be traced back to facilitate inventory management and
material supply and demand.
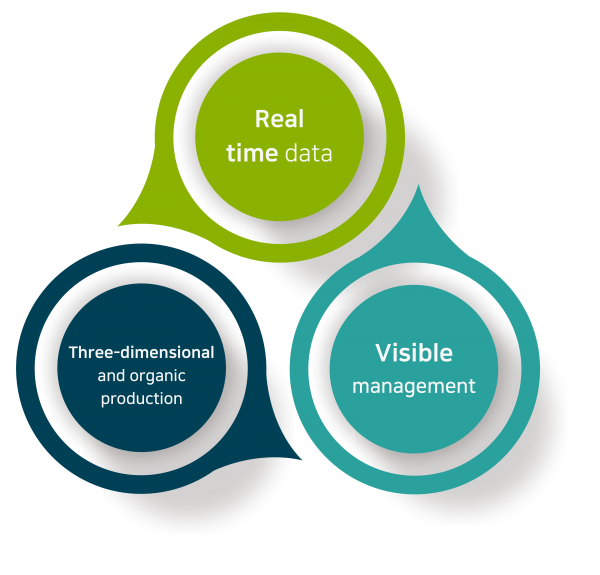
Characteristic
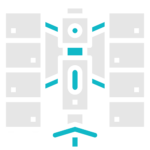
Real-time data collection
It collects data in real time using a dedicated terminal and sensor network. In addition to various production environment data such as pressure, temperature, speed, voltage, and current, it is possible to simultaneously collect and analyze a variety of data, including bar code information, automatic collection of quality measurement data, and machine operation history, including quality status and machine operation history.
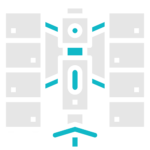
Order-manufacturing-shipping in one pass
You can register sales order information and manage it by linking it with production products. Based on the registered order history and production targets, resource requirements can be calculated quickly and easily. Even if production conditions suddenly change, such as urgent orders, non-stocking of materials, and manpower fluctuations, you can respond quickly by modifying the production plan.
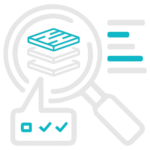
Lot tracking
Systematic management of material and process flow. When producing products, you can instantly see who, when, in what materials, in what machines and in what working environment. In addition, it minimizes the control range in case of defects by tracking which products were produced with.
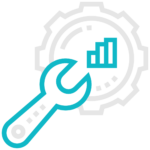
Interlock
It provides a strong interlock to maintain a high quality system. In case of failure to comply with established quality procedures such as process omission, inspection omission, first-in-first-out violation, the system fundamentally blocks them and controls product flow to prevent defects and malicious inventory.
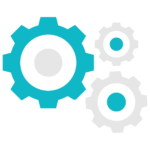
Easy and convenient active system
It is an active system guided by the system so that users can use it easily and conveniently. It provides optimum convenience of use based on the experience required by various users.
l Expectation effectiveness
– With the introduction of FactoryView™ MES, global manufacturing competitiveness can be secured through innovative effects of
productivity improvement, quality improvement, and cost reduction.
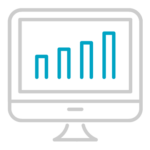
quality improvement
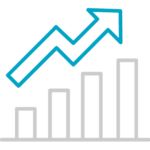
more equipment
uptime
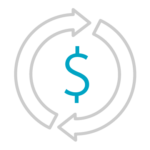
manufacturing cost
decrease
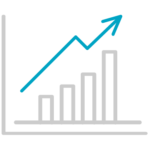
Increased productivity
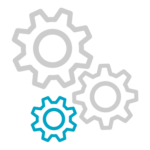
OEE improvement
l Expected effects of introducing FactoryView™
l 주요 기능 화면
[masterslider id=”4″]
*판매계획과 판매 적중률을 관리합니다.
*수주를 등록하고 현황을 분석합니다.
*창고 입출고 수불 및 재고를 관리합니다.
*제품출하를 등록하고 각종 출하상황을 분석합니다.
[masterslider id=”2″]
*주생산계획 MPS를 산출합니다.
*제품별/설비별 작업지시를 관리합니다.
*생산지시대비 실적현황을 분석합니다.
[masterslider id=”3″]
*설비별 생산실적, 불량, 자재사용 실적을 등록합니다.
*로트이력에 대해 정전개/역전개로 추적합니다.
*공정이동표를 발행하고 로트분할을 수행합니다.
*작업일보를 관리합니다.
*공정, 설비, 작업자의 실적을 분석하고 관리합니다.
*공정품질검사 수행여부를 확인하고, 측정데이터를 관리합니다.
*품질통계를 산출하고 추이를 분석합니다. (X-r, 정규분포도, 공정능력)
*부적합 등록 및 처리를 수행합니다.
*원자재, 부자재의 입출고를 관리합니다.
*자재재고를 조회하고 수량을 조정합니다.
*설비일상점검과 예방보전을 수행합니다.
*설비고장 및 수리현황을 관리합니다.
*설비 예비품 입출고, 재고현황을 관리합니다.
*설비 보전지표를 분석하고 관리합니다.
OEE (Overall Equipment Effectiveness)
*설비종합효율을 산출합니다.
-시간가동률
-성능가동률
-양품률
-설비종합효율
*종합효율추이를 관리합니다.
*금형의 세트를 구성하고 입출고 현황을 관리합니다.
*금형재고와 현장 출고된 금형현황을 조회합니다.
*금형사용이력을 조회합니다.
*금형의 수명을 분석합니다.
ㅣ 생산실적관리



수주를 등록하고 현황을 분석합니다.
ㅣ 영업관리



수주를 등록하고 현황을 분석합니다.