MachineView™
(Force, AE, A, Multisensing)
Error proof Solution
MachineView™
(Force, AE, A, Multisensing)
This is a monitoring device that measures the pressure applied to equipment during the plastic forming process, analyzes the patterns, and notifies the operator while stopping the equipment in the event of a defect to prevent continuous defects.
MV880
MV880 is mainly applied to medium and large facilities, cold/hot formers, and multi-stage formers with 5 or more stages.
It is a top-notch model with various advanced functions such as AI monitoring, mold management, and smart factory big data collection.
MV550
MV550 is mainly applied to small and medium-sized equipment, cold formers, presses, and thread rolling machines.
It is composed mainly of monitoring functions, and advanced functions and additional functions are excluded to minimize the burden of initial introduction cost.
Why
should we use a
process monitoring monitor?
- Since it is impossible to check the occurrence of defective products in real time, all LOT is inspected, which takes unnecessary time and money.
- Defective products are produced because the troubles in the process cannot be grasped in real time, resulting in quality troubles and delays in delivery.
- Tool breakage can damage the machine, increase the cost of tool, and cause poor quality.
- It takes a lot of manpower and time and hinders factory automation because one operator has to be dedicated to one machine to monitor the process for any troubles.
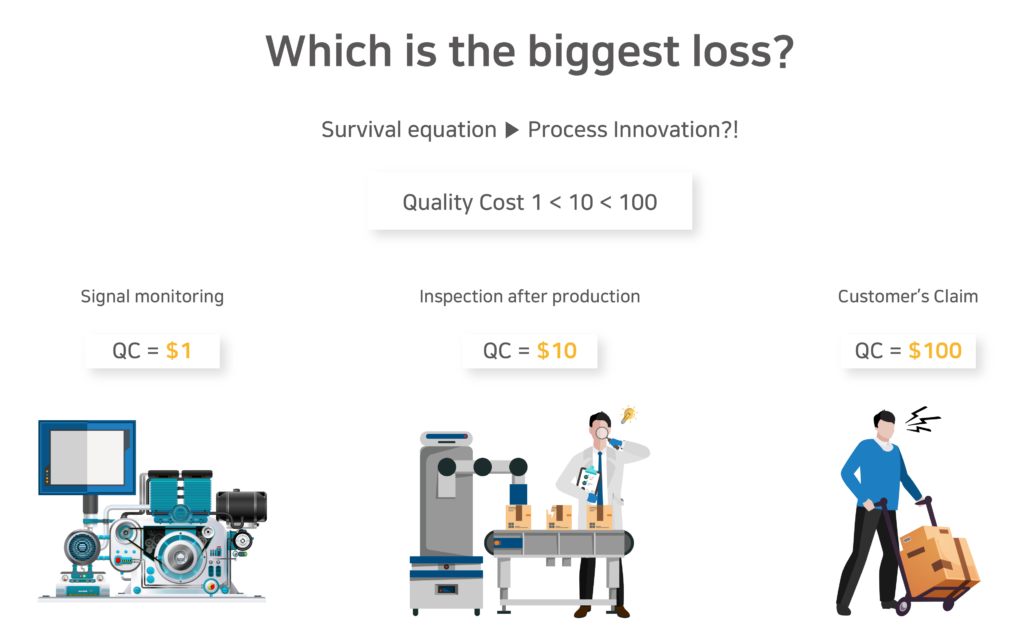
MachineView™ is
“ With the introduction of the MV880 that uses artificial intelligence to automatically monitor processes, you can improve your productivity and quality through real-time production data collection and quality inspection, and reduce manufacturing costs. ”
Why
use 3View’s MachineView™
rather than other process monitoring monitors?
Differentiation
The defect detection capability and productivity of a process monitoring monitor are inversely proportional to each other. If the defect detection ability is strengthened, the equipment stops more frequently.
Productivity will drop, and if productivity is emphasized, defect leakage will occur more frequently, increasing quality costs.
However, 3View’s MachineView™ does not detect defective products by simply reducing the range of error that is judged as defective, but AI precisely analyzes the pattern of the signal to analyze changes in the molding process in detail.
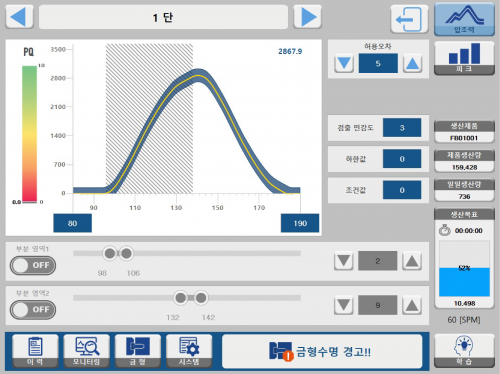
Enhance defect detection
capability with AI
Existing process monitoring monitors were
considered good if the forming force was within tolerance.
However, MV880 can be immediately judged as a defective product
if a forming force pattern different from that of the existing product is detected, even though the Forming force is within the tolerance range through a proprietary pattern analysis algorithm through AI.
* This function is only applicable to the MV880.
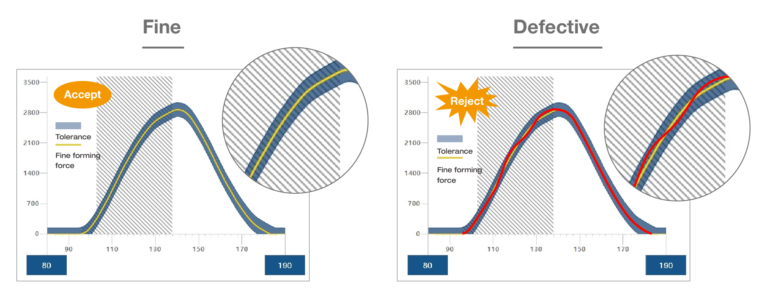
Check process state
changes using Machine learning
Self-collecting and learning product molding data, as well as changing the conditions of the machine over long periods of operation.
It provides a range of Forming force that can clearly detect defective products without hindering productivity by learning the conditions of production of goods, and automatically calibrates the real-time monitoring conditions by learning the temperature changes or process characteristics of the machine to prevent unnecessary macine shutdown.
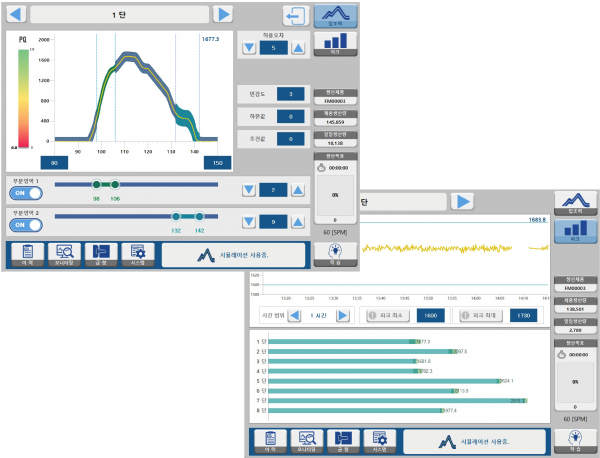
01 _ AI Teaching to detect precise forming conditions
02 _ Easy-to-use operation
03 _ Barcode scanner, various digital meter connections
04 _ Product management, tool life management
05 _ Supports building up smart factory system
by interface with FactoryView™ package
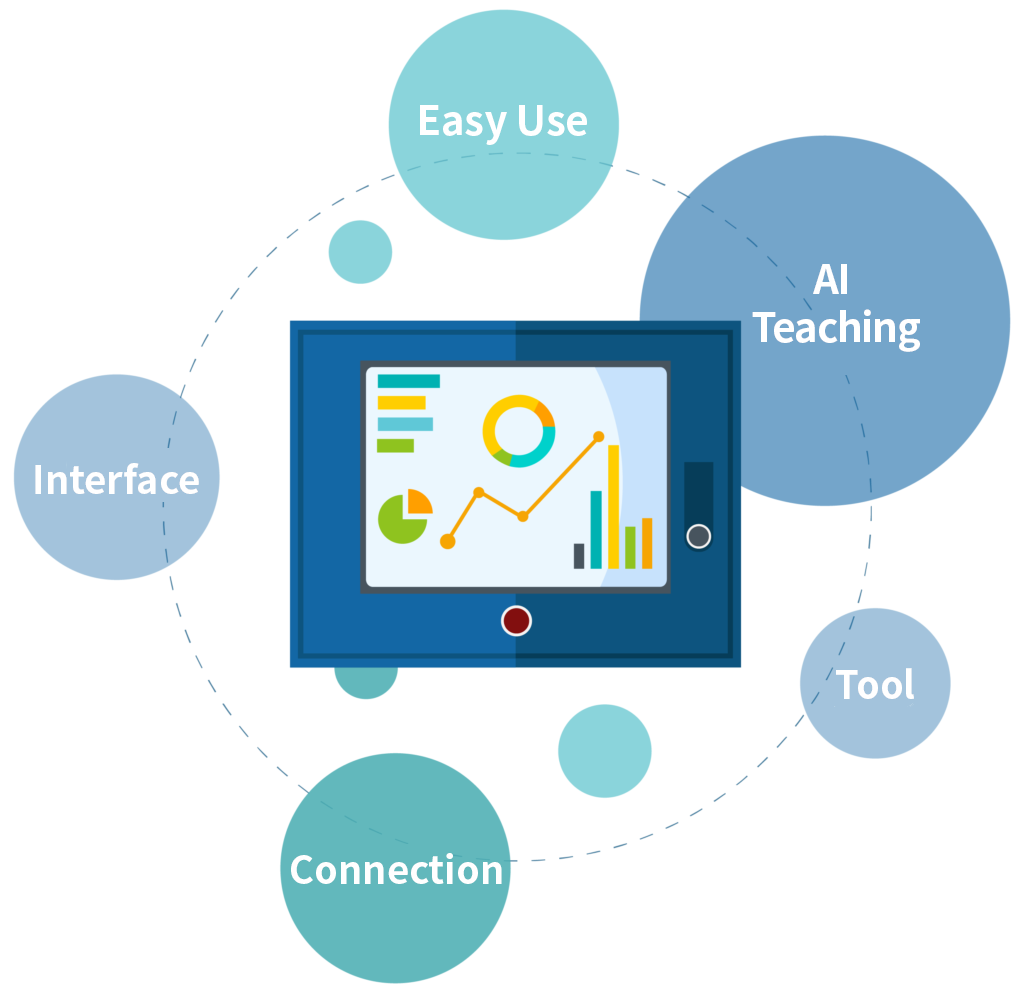
- As is
- Poor quality, quality deterioration
- Increased cost of rework, quality inspection
- Delay in delivery due to reduced production efficiency
- Systematic process control not possible
- Overstock aginst tool damage
- Unable to determine cause of defect, recurrence of defect
- One machine dedicated to one operator
- Writing and collecting work journals by handwriting
- To be
- Real-time pressure monitoring / control
- Forming force trend analysis
- Detection of defective products by AI
- Machine learning capability to learn(teaching) production conditions
- Tool life management life expectancy forecast
- Fault detection History Analysis
- Output management / support for unmanned manufacturing
- Interworking SPC, POP, and MES system
l Expectation effectiveness
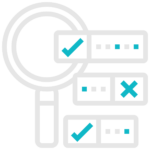
Reduce quality costs by early detection
of defective products
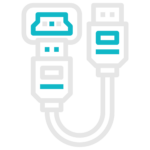
Quality improvement through forming force analysis and defect history analysis
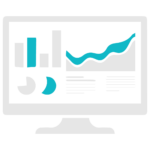
Production process management
linked with FactoryView™